海外(ミャンマー バゴー川)における大土被り・高水圧・河川横断・長距離推進 現場報告
はじめに
本工事は、東南アジアのインドシナ半島西部に位置するミャンマー連邦共和国の最大都市ヤンゴン市内において、ヤンゴン都市圏の上水道施設の拡充を目的とした導水管(呼び径700NS形ダクタイル鋳鉄管)敷設のため、バゴー川横断部のさや管管路を呼び径1100の推進管を使用して泥水式推進工法で築造するものです。
工事概要とその特徴
工事名 | GREATER YANGON WATER SUPPLY IMPROVEMENT PROJECT(MY-P5) CONTRACT PACKAGE:ICB-03 CONSTRUCTION OF BAGO RIVER PIPELINE CROSSING |
工事場所 | ミャンマー連邦共和国ヤンゴン市 |
発注者 | YANGON CITY DEVELOPMENT COMMITTEE(YCDC) |
施工者 | 戸田建設株式会社 |
工法 | アルティミット泥水式推進工法 |
管呼び径 | 1100 |
管種 | 高耐水圧対応推進管 J-MAX推進管(90N1種) 継手性能0.3MPa |
推進延長 | L = 814.59m |
線形 | 直線、勾配レベル |
土被り | H = 31.625m(発進) ~ 31.635m(到達) |
土質 | シルト質砂(最大N値34)、シルト粘土(N値8) |
発進立坑 | セグメント式立坑 内径 8000 |
到達立坑 | セグメント式立坑 内径 5000 |
推進期間 | 2019年 1月23日 ~ 2019年 4月27日(発進鏡切断~掘進機回収) |
図-1.ヤンゴン市位置図 図-2.平面図 図-3.縦断図
推進管路は発進してから約100mで河川下となり河川横断距離は約650mで、河川最深部での離隔が約5mとなっています。
課題と対策
大土被りおよび高水圧、河川横断、長距離推進と厳しい条件が重なった本工事の主な課題と対策は次のとおりです。
掘進機の選定
掘進機の選定における課題は次のとおりです。
- 想定最大自然水圧0.3MPaに対応する水密性の検討。
- 発進および到達でのCJG工法による地盤改良区間での閉塞の防止。
- 到達側約100mのシルト粘土による面板閉塞の防止。
当社掘進機の駆動部および中折れ部シールの耐水圧が0.3MPaであることから特別な改造は行わないこととしました。
掘進機タイプは礫破砕型とすることで切削片による閉塞を防止するとともに、高トルクによって改良体強度が比較的大きいと想定される発進側改良区間の安定した掘進が可能になります。
また面板開口率を普通土用よりも大きくとることで固結シルトに遭遇した場合でも取り込みやすくなり面板閉塞発生の可能性を低くできると考えられます。
ただし、固結シルトを取り込む際に礫破砕用コーン部での目詰まりが発生する可能性があることから、面板正面から補助的に送水するための配管ラインを設けました。
ビット配置については地盤改良工法および推進延長を考慮して先行ビットは強化型シェルビットを採用し、掘削軌跡を全断面確保する配置とし、外周ビットについても強化型ビットを配置しました。
写真-1.泥水式掘進機全景 写真-2.掘進機面板
発進坑口設備
発進坑口設備の課題は次のとおりです。
- 高い水密性を有すること、またその性能を推進完了まで保持できること。
- 止水ゴムの捲れ(反転)防止。
- 坑口コンクリート壁の剥離防止。
止水ゴムについては水密性に優れその形状から捲れにくい厚さ20㎜の耐摩耗性ゴムのL型パッキンとしました。
また、捲れ防止措置としてスライド板は降ろした状態で板同士の隙間を10㎜程度とし、スライド板を調整する際に止水ゴムの締付の緩みを防止するために二重締付構造としました。
ただし、止水ゴムが捲れることはなくても何らかの原因により止水ゴムが浮いた場合はそこから土砂が噴出することも考えられるため、止水ゴムを抑える補助的な設備として特殊シール材を使用した当社独自のシールチューブ式発進坑口を採用しました。
坑口コンクリート壁の剥離防止対策として、L型に加工した異形棒鋼を立坑セグメントから溶接で立ち上げてコンクリートを打設する計画としました。
また、万が一コンクリート壁から噴出等が起こった場合の対策として坑口内部に注入するための注入孔を配置しました。
バッキング対策
推進管は呼び径1100と小さい径ですが、大土被りであることから必ずバッキングすると考えました。
想定バッキング力は502kNとして防止設備について検討した結果、推進管にM24インサートを設けてボルトで反力金具を取り付けるインサートアンカ方式を採用しました。
また、バッキング防止対象推進管についてはインサートを設けるために、カラー長を通常より長くしました。
バッキング防止反力は支圧壁からフレーム方式でとるのではなく、発進架台に反力金具をボルト固定する計画としました。
写真-3.シールチューブ式発進坑口 写真-4.バッキング防止設備
長距離対策
長距離推進の施工に対する課題は次のとおりです。
- 地下水の塩分によって滑材が希釈劣化されることによる周面抵抗力の上昇
- 何らかの原因による推進力の上昇
- レーザ可視距離限界後の管内測量作業の軽減
周面抵抗力を低減するためにアルティミット自動滑材注入システム「ULIS」による1次・2次滑材注入方式を選定し、1次と2次滑材ともに高粘性滑材「アルティーK」を採用しました。
また、地下水の塩分濃度による影響評価から配合量を標準配合の1.25倍にする計画としました。
推進力検討の結果、元押のみでの施工が可能となりましたが、予期せぬ推進力の上昇や到達後の縁切りのことも考慮して中押設備を2段配置する計画とし、さや管管路であることから特殊中押を採用しました。
また、S管とT管接続部から出水した際の対策として、T管外周面の止水ゴムの地山側に特殊シール材を使用したシールチューブを配置しました。
管内測量作業を軽減するためにジャイロコンパスおよび液圧差レベル計測システムを採用しました。
両システムを併用することで掘進機の位置を想定することが可能となります。
また、管内設備の配置をハンガーを使用することで有効スペースを確保する計画としました。
写真-5.ULIS制御盤および管内バルブユニット 写真-6.高粘性滑材アルティーK
河川横断
河床最深部での離隔は約5mであり、ここで河床を抜いてしまった場合は逸泥を引き起こし切羽圧力の保持が難しくなることが想定され、対策案は次のとおりとしました。
- 海の干満により河川の水位差が6m程度あることから、切羽圧力は自然水圧をこまめに確認して決定する。
- 泥水粘性についてはファンネル測定で28秒から30秒を確保する。
- 土量の体積管理は推進管1本の土量はもとより、1本ごとの変化を確認する。
- 有事の際は掘進機前面への送水ラインから切羽に固結滑材を注入する。
到達方法および設備の検討
到達坑口設備の課題は次のとおりです。
- テールボイドからの出水
- 止水ゴムの水密性およびその締付方法
施工条件から考えれば鏡切断から掘進機押し出しまでを立坑内に注水して潜水士による水中作業とすることが最も安全な作業方法であると考えますが、海外での施工であることや大量の清水の確保が難しいことから、作業方法を次のとおりとしました。
- 鏡切断は気中にて行う。
- スキンプレートが止水ゴムにかかるまでは到達坑口を回収筒としての水中押し出しとする。
- 回収筒内押し出し完了後は到達架台を設置し、立坑内に注水して掘進機を押し出し、立坑内排水後に切り離し回収する。
テールボイドからの出水対策として到達手前20mからは1次滑材を固結滑材に変更する計画としました。
到達ゴムについては止水ゴムを2段構造とし、その締付方法は水中押し出しを計画していることから発進坑口と同様に特殊シール材を使用したシールチューブ方式を採用しました。
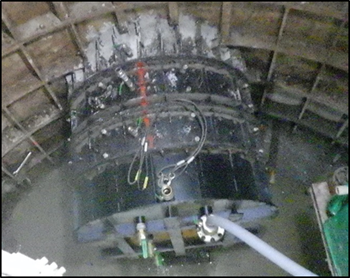
施工報告
発進鏡切断
試験孔からの確認の結果、砂が噴出しましたが地盤改良業者の懸命の止水作業により無事に鏡切断を終えることができました。
初期掘進
改良体が非常に硬くカッタトルクの上昇と掘進速度の著しい低下が発生しましたが、懸念された切削片による閉塞は発生せず連続掘進を行うことができました。
改良体から地山に変化する際も心配された取込過多は確認されませんでした。
なお、バッキングについても計画どおりの設備により、バッキングの発生やトラブルはありませんでした。
写真-8.管路上部 写真-9.初期掘進状況
本掘進
前項で記述した課題と対策を含めた施工内容は次のとおりです。
- 発進坑口止水ゴムと推進管の間から地下水が噴出
シールチューブの加圧膨張により噴出を止めることができました。
この現象はその後も続き、その都度同様の手法で止めることができたことから、L型パッキンは水密性には優れているがその形状からストレート型に比べ張力が弱く止水ゴムが浮きやすいのではと推察します。 - 縁切り推進力のみの上昇
滑材注入量の不足と滑材の希釈劣化によりテールボイドが良い状態で保持されていないと考え、ULISによる2次滑材注入量の変更、滑材の追加注入の実施、また滑材の配合量を計画の1.25倍から1.5倍に変更しました。
対応後は縁切り推進力も上昇前の値まで下がり、最終推進力も計画値以下で推移しました。 - 河川最深部の横断
泥水管理および体積管理を徹底しながら通常どおりの掘進作業を行い、無事に通過しました。
通過後も自然水圧の変化や推進力の急激な上昇といった変化はありませんでした。 - 土質の変化
想定どおりシルト質砂の状態が続きましたが、シルト粘土への変化は想定よりも早く到達手前約170mの位置で始まりました。
ただし、粘土が排土され始めてからは計画どおり切羽に清水を送水することで著しいカッタトルクの上昇や掘進速度の低下は発生しませんでした。 - 推進力の上昇
土質が変化して40m程度掘進した辺りから推進力がじわじわと上昇し始めたためテールボイドが確実に造成されていないと考え、掘進速度を抑える等の対策を試みましたがその後も推進力の上昇は続きました。
また、発進坑口止水ゴムと推進管の間からの出水も頻繁に発生し、その都度シールチューブの加圧膨張や管内からの固結滑材の注入を行う等の作業を続けながら到達しました。
最終推進力は5,780kN(計画値の90%程度)でしたが、縁切り推進力は計画値を10%程度上回った7,050kNでした。 - 自然水圧
自然水圧は最大で0.29MPa、通常は0.26~0.28MPaと計画どおりの値で推移しました。 - 推進精度
到達精度は上30㎜右15㎜でした。
管内測量は計画通りジャイロコンパスと液圧差レベル計測システムを併用していたためその頻度は抑えることができました。
ただ、管内の有効スペースを確保し台車を使用していたとはいえ、この推進延長での管内測量は想像以上に大変過酷な作業でした。
写真-10.発進基地全景(発進立坑) 写真-11.発進基地全景(プラント設備)
到達
前項で記述した課題と対策を含めた施工内容は次のとおりです。
- テールボイドからの出水
試験孔からの探査では湧水はなく、回収筒内で止水ゴムを損傷しないよう外周ビットを全て切断撤去し回収筒設備を行うことができました。 - 掘進機押し出し
元押または第1中押でも縁切りができず、第2中押の油圧ジャッキを第1中押に増設することで縁切りが可能となりました。
なお、中押作動時に心配されたS管とT管接続部からの出水はなく、シールチューブを使用することはありませんでした。 - 掘進機回収
掘進機と後方筒の押し出しともに第1中押を併用しての作業となり想定以上の時間を要しましたが、幸いテールボイドからの出水はなく、計画とは違い立坑に注水しての水中押し出しは行わずに掘進機と後方筒を無事回収することができました。
写真-12.掘進機押し出し状況 写真-13.掘進機吊上げ回収状況
おわりに
本工事は難しい条件が重なったうえに海外での施工ということもあり、事前に施工および資機材について検討を重ねましたが、それでも改善すべき点や想定しきれなかった部分がありました。
これらの項目については今後の施工に活かしたいと考えております。
また、今回は日本人技術者は必要最低限の人員とし、現地作業員を交えての施工となりました。
当初は推進工法自体を知らないことや言葉の問題等色々と不安がありましたが、ミャンマー人は日本人と気質が似ているのか非常に勤勉で多くのことを習得しようと日々頑張っている姿に感銘を受けました。
最後に、戸田建設(株)をはじめご協力いただいた関係者の皆様にはこの場を借りてお礼申し上げます。