急曲線推進用特殊継手の強度実証試験について
はじめに
推進工法は、社会的要求に応えるために多くの技術開発が進められ、長距離・急曲線推進施工を可能にしてきました。
施工において解決しなければならない課題の中には、推進管が曲線部において計画線より外側にせり出すという挙動や隣接する推進管が曲線の内側で局部接触するため管が破損するというものがあります。
アルティミット工法では、これらを解決するために、急曲線対応掘進機の開発や掘進機が造成した曲線に推進管を理想的に追随させるセンプラカーブシステム、管継手部の止水性を確保しつつ急曲線における追随性をさらに高めた特殊継手が開発されています。
今回、特殊継手の規格化にあたり、特殊継手の設計の再検討と、計算どおりの強度を有しているかを実証するための強度試験を行いました。
特殊継手の開発経緯
アルティミット工法では、曲線推進においてはセンプラカーブシステムが採用されます。
センプラカーブシステムは、推進管の継手部ごとに塑性領域の広い推力伝達材(センプラリング)を上下対称に設置して、推進力の伝達位置を管の中央部に維持することによって、掘進機に対する追随性をよくすること及び、曲線内側の管端部の接触を防止することを特徴としています。
しかし、超急曲線の場合には、推進管継手部の屈曲による曲線外側へのせり出しや曲線外側の目地開口長が大きくなり止水性が確保できないという問題が発生していました。
このような問題点を解消するため、超急曲線でも推進管継手部の屈曲を小さくし、止水性を確保できる機構の検討が行われ、センプラリングを併用した特殊継手が開発されました。
推進管の継手部に前端面と後端面の上下対称位置にセンプラリングを設置した特殊継手を配置することにより、継手部の開口を2箇所に分散させることが可能になりました。
この結果、従来に比べ曲線外側の管開口長が約1/2となり、特殊な短尺管ではなく、JSWASで認定された推進用ヒューム管で安全に急曲線施工を行うことが可能になりました。
強度実証試験の目的
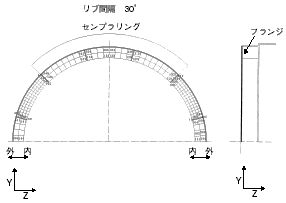
急曲線推進用特殊継手を採用した施工事例が増えてきましたが、特殊継手は、比較的余裕を持たせた構造で設計・製作されていました。
このたび、特殊継手の規格化にあたり、有限要素法により解析し、軽量化とコスト縮減を図った特殊継手の設計を完了しました。
強度試験はこの特殊継手が、計算どおりの強度を有しているかを実証することを目的として実施しました。
図-1、表-1に設計、検討結果の一部を示します。
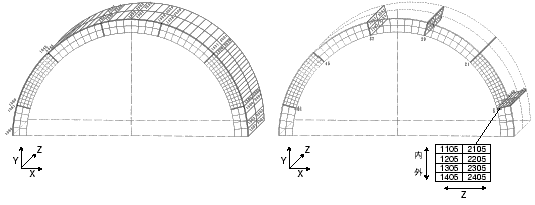
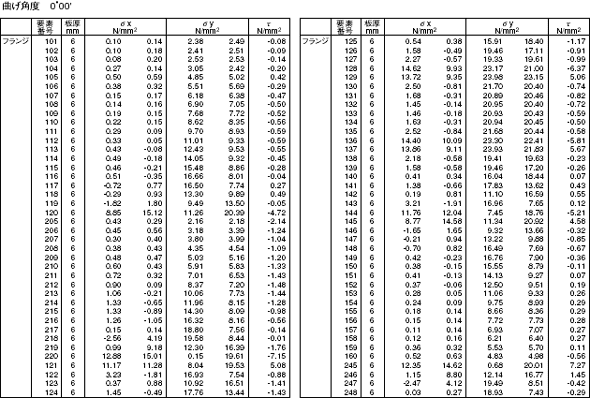
強度実証試験
試験日時
2002年12月24日~25日
試験概要
載荷試験の回数
試験用供試体(呼び径1000mm用特殊継手)を2個製作し、左右1回ずつ合計4回の載荷試験を行いデータを採取しました。
特殊継手の仕様は、図-2に示すとおりです。
データの採取
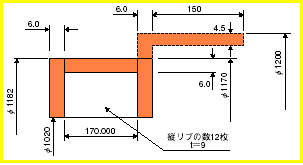
載荷圧力の読み取り
供試体の歪み量(箔歪みゲージ使用)
垂直歪み量(ダイアル式変換器)
試験方法(図-3)
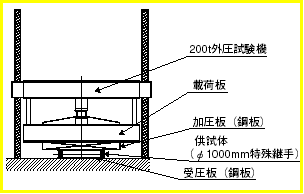
載荷試験は、水平加圧方式で行いました。
試験状況
試験は、呼び径1000mmの特殊継手の外板(スティール部)に鋼製用歪みゲージ(3軸65mm)を、内側コンクリート部にはコンクリート用歪みゲージ(3軸65mm)を設置番号表に従い配置しました。(写真-1)
データの記録には、 東京測器研究所のデータロガーTDS-303とスイッチボックスSSW-50Cを3台使用しました。(写真-2)
外圧試験機からの荷重の出力には、東京測器研究所のロードセル(CLP-2MNB)を、特殊継手圧縮時のたわみ測定には、CDP-100型変位計を使用しました。(写真-3)
載荷時の特殊継手内側部コンクリートの状況を確認するために、コンクリート用歪みゲージ(3軸65mm)を取り付けました。
載荷重圧面には、 100mm×100mm×10mm 1.7倍発泡のセンプラリングを設置して載荷しました。(写真-4)
写真-1 歪みゲージ配置 写真-2 記録装置の配置 写真-3 載荷状況 写真-4 載荷時の内面
試験結果(呼び径1000mm用特殊継手)
歪み測定位置
図-4 歪み測定位置図 図-5 a-a断面(耐荷試験図)
コンクリート
設計基準強度 | 50N/mm2 |
ヤング係数 | 37000N/mm2 |
ポアソン比 | 0.2 |
許容引張応力 | 3.91N/mm2 |
鉄板
ヤング係数 | 210000N/mm2 |
ポアソン比 | 0.3 |
許容曲げ応力 | 140.00N/mm2 |
リブ角度 | 30° |
リブ厚 | 9.0mm |
フランジ厚 | 4.5mm |
スキンプレート厚 | 4.5mm |
センプラリング
載荷幅(角度) | 100mm |
載荷面積 | 7569mm2(10.56°) |
荷重強度 | = 載荷重 / 7569(N/mm2) |
コンクリート応力 | = 歪み × 補正係数 × 37000(N/mm2) |
鉄板応力 | = 歪み × 補正係数 × 210000(N/mm2) |
破壊荷重強度 | (N/mm2) |
測点 | 1 66.65 |
2 67.31 | |
3 89.91 | |
4 81.91 | |
平均 76.36 |
本試験結果及び考察
荷重強度は、載荷重を載荷面の面積で除したもの、応力は、歪みにヤング係数を乗じ補正したものです。
今回の試験では鉄板とコンクリートの付着程度が未知数であったため、コンクリートの引張力は鋼部分のみで負担するものとしました。
目視では確認できませでしたが、実際に荷重を載荷したコンクリート部分の測点では、設計荷重(25N/mm2)に達する前に、細かいひび割れが発生していたと思われます。
しかし、鉄板が荷重強度σx=60N/mm2付近で降伏するまではひび割れの発生のみに留まり、コンクリート本体部分に支障が出ることはありませんでした。
今回の試験結果では、破壊時荷重強度は平均で76.63N/mm2となりました。
これは設計荷重強度の2.18倍(1.9~2.56倍)であり、強度的には問題ないと考えられます。
コンクリートにひび割れが発生した原因としては、図-4に示すように供試体の上下に設置したセンプラリング(100mm×100mm)の面積分のみでコンクリートに力を伝達させたため、センプラリング両端で大きな引張応力が発生したことによるものと考えられます。
しかし、実際の施工においては、センプラリングは円周方向に所定の長さを持った形状で設置するため、荷重は広く分布されて集中応力となることはありません。
また、センプラリングの両端部に発生する引っ張り応力に対しては、センプラリングの両端部分にリブ材を設けることによって解決できます。
なお、今回製作した特殊継手に使用したコンクリートは、高強度コンクリートで50N/mm2 のものを手詰め転圧して製作しました。
同コンクリートのテストピースの圧縮強度は、50N/mm2~51N/mm2でした。
本試験の結果から、今回設計・規格化した特殊継手の強度、剛性は十分であると考えられます。
また、コンクリート材の圧縮強度や引張強度を上げる添加剤の研究を進めることによって、特殊継手の性能をさらに上げ、より安全性の高い曲線施工を提供できると考えます。